Despite centuries of innovation, no one has devised a more useful and adaptable medium-sized container for liquids and semisolids than a cylindrical container. Its shape, based on the circle, provides maximum strength; when fully laden, it can be tipped over and rolled. Early ocean shippers employed heavy, easily breakable clay and ceramics. They knew smelting and metal working, but evidently could not produce metal containers much larger than pots and pans. From the Middle Ages until recent times, the standard container material was wood, usually oak, formed into metal-bound, stave-constructed barrels and kegs (see Barrels). The wooden barrel had no weight advantage but was far stronger and could be manufactured anywhere of materials widely available at low cost. Design differed little from the early jars, featuring the same bilged sides for maximum strength. In almost every trading nation, the wooden barrel reigned as the universal shipping container for liquids and semisolids until the late 19th century, when the first steel barrels appeared in Europe.
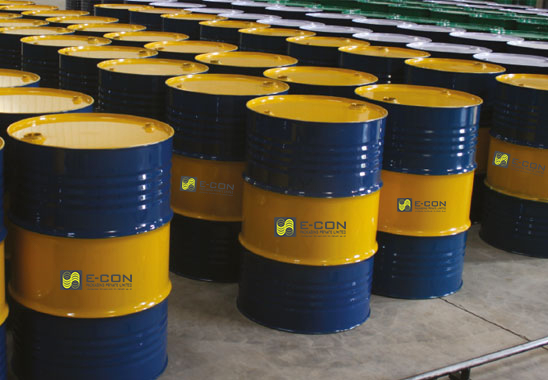
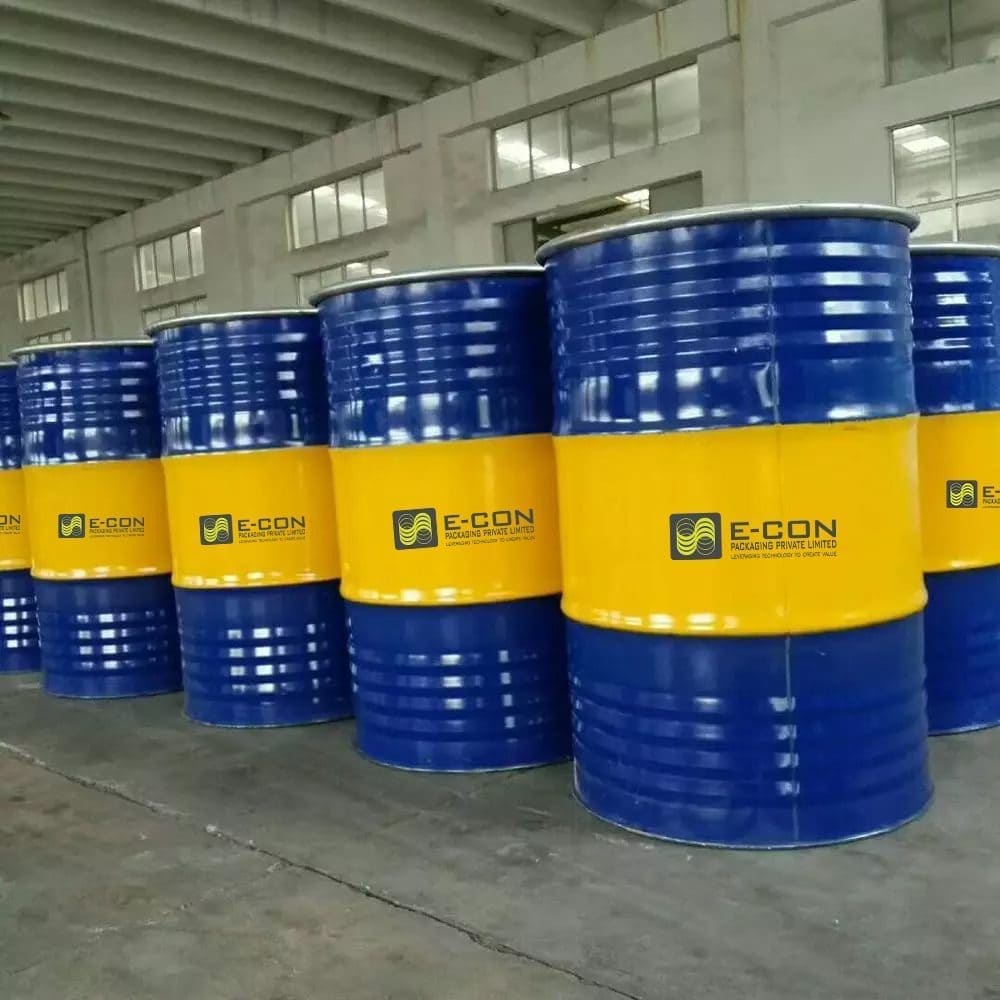
Impetus for the invention and development of the modern steel drum had begun years earlier with the Great Oil Rush of 1859. Oil-drilling technology improved so rapidly that by 1869 U.S. wells were producing 4,800,000 barrels (7.6 x 105 me) a year. That introduced a much tougher problem: how to store and ship the oil. The only container available was the wooden barrel. Demand soon outstripped the production capacity of the cooperage firms, and oak became scarce and very expensive. The immediate solution wasthe development of pipelines, railroad tank cars, and the tank truck. But for smaller packages, oil-industry shippers still had to struggle along for another 40 yr with the time-honored wooden barrel. Kerosene was the most important barreled product. The wooden barrel’s chief problem was leakage. Designed to hold 50 gal (0.189 ma), it commonly lost enough per trip to arrive at its destination containing only about 42 gal (0.159 ma), a figure that has remained the standard “barrel” measurement of the oil industry.
A few years after their development in Europe, the first steel barrels were produced commercially in the United States by Standard Oil at Bayonne, NJ, in 1902. Constructed from 12-14 gauge terne steel, they were heavy, clumsy, bilged affairs with riveted or soldered side seams, and were anything but leakproof. Extremely rugged, many of them lasted 20-30 years. They were also expensive compared with wooden barrels. Despite the need, steel barrels were slow to catch on; yet technical developments came rapidly. In about 1907, the welded side seam was introduced, which curtailed the leakage problems of riveted barrels and reduced costs. Shortly afterward, the first true 55-gal (208-L) drum was introduced, its characteristic straight sides contrasting markedly with the bilged barrel. Rolling hoops were introduced soon thereafter, both expanded and attached, the latter utilizing an I-bar section. The mechanical flange was invented after 1910. These improvements were far-reaching and gave the new container added advantages. Among them was lighter weight, which reduced shipping costs and reduced the amount of steel required. The new drum design permitted use of 16 and 18-gauge steels instead of the far heavier gauges used previously. These drum developments were followed in 1914 by the first true steel 5-gal (18.9-L) pail featuring the first lug cover.
The use of steel containers grew slowly before 1914, despite their cost, weight, and safety advantages over wooden containers. The advent of World War I marked the beginning of the end for the wooden barrel, and the eventual dominance of the steel drum and pail. Wartime demand also spurred many improvements in manufacturing techniques and equipment. After the war, many innovations appeared, including pouring pails, agitator drums for paints, and new, colorful decorating techniques. Manufacturers began to use steel containers for products other than petroleum products and chemicals. Toward the end of the 1930s, the steel-container industry started gearing up for a second wartime effort. This time, however, the demands were far more stringent, requiring fuel containers for a highly mechanized war on more than one front. Innovation took a back seat to production considerations as war machines on the ground and in the air consumed vast amounts of fuel and chemicals.
The 55-gal (208-L) 18 and 16-gauge drums were indispensable to the fuel supply of island bases and assaults in the Pacific, frontline mechanized operations in Europe, and to air and ground operations in East Asia. Apart from its ruggedness, the fact that a cylindrical drum could be rolled by one man was an important feature.
Although a downturn in steel drum and pail production occurred at the end of World War II, it was of short duration. Resumption of business created a demand from industry, agriculture, and consumers. The acceleration in chemical and pharmaceutical product development and output provided new markets for steel drums and pails. Demand for paints, lacquers and varnishes, adhesives, inks, foodstuffs, and other products made the steel shipping container industry one of the largest users of cold-rolled sheet steel (approximately 1 million tons in 1993). Despite the introduction of competitive containers made of other materials and of intermediate-bulk containers, U.S. production increased from 2.4 million drums in 1922 to 32.35 million drums in 1993.
Drums range in size from 13 to 110 gal (49-416 L), but the 55-gal drums account for 80% of annual production. Over 75% of all new drums are used for liquids and the rest, for viscous and dry products. About 70% of the market is accounted for by five broad product categories: chemicals (35%); petroleum products, including lubricants (15%); paints,coatings, and solvents (10%); food and pharmaceutical products (5%); and janitorial supplies, cleaning compounds, and soaps (5%).
As a result of increased environmental awareness, drum manufacturers, drum users, reconditioners, pail and drum recyclers, and steelmills have developed programs to collect, recondition, and/or recycle used steel drums and pails. In addition the recycled content of steel has surpassed an average of 25% per container. In fact, more steel is recycled than all other packaging materials combined (53 million tons of steel scrap in 1993) (1). Thus, choosing steel packaging conserves energy and natural resources and reduces waste. Each year over 40 million drums are reconditioned, thus prolonging the useful life of steel drums.
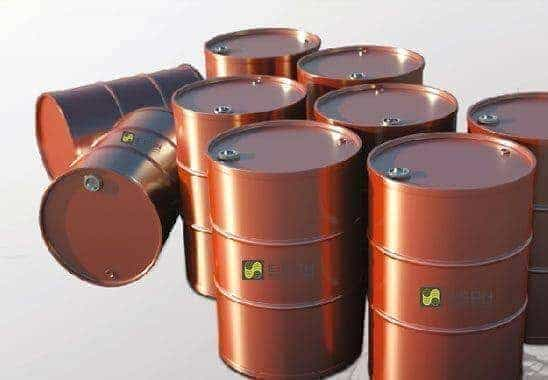
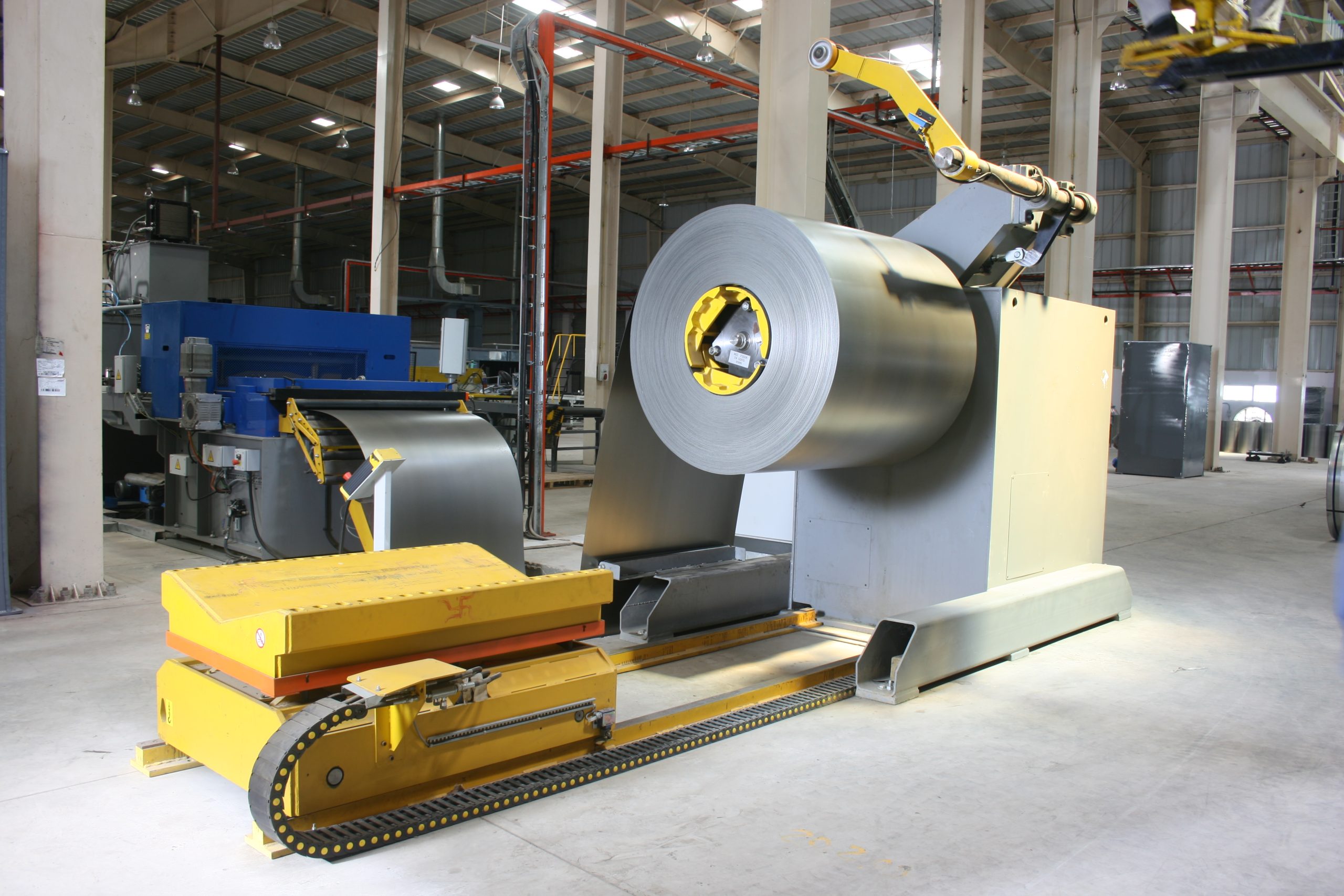